Types Of Label Adhesives And Their Properties
With many different options available, knowing you’re getting your labels printed with the right adhesive is crucial – especially when all you want is a label that "just works."
.
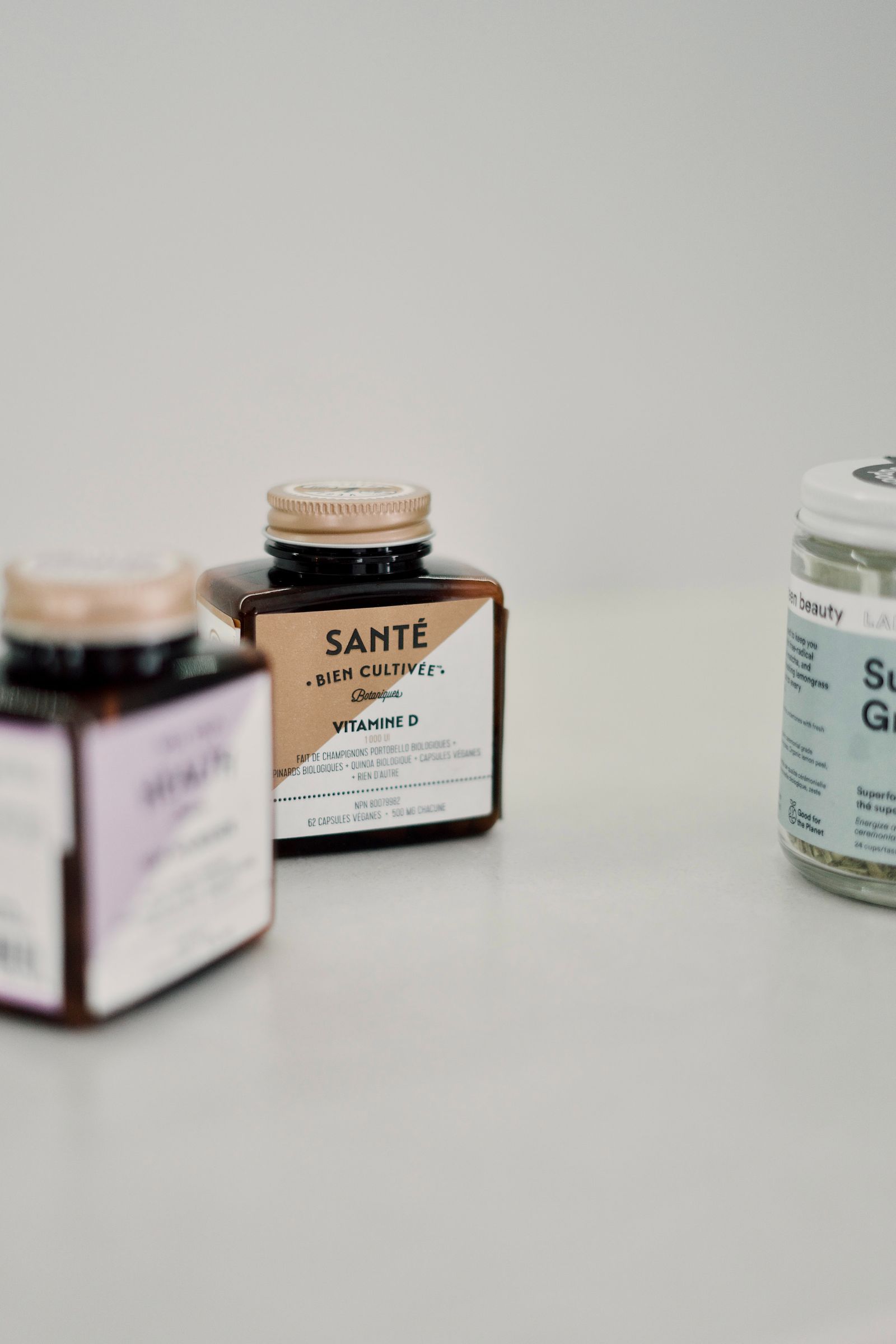
.
Types of Label Adhesives
There are three main classifications of adhesives to know: permanent, removable and repositionable. Within those categories, pressure-sensitive adhesives have different properties that vary from one to the next, but we’ll get to that in a bit. First, let’s learn more about adhesive types and the reasons why they’re used.
.
- Permanent: The majority of labels printed use a permanent adhesive because they work for most label applications and tend to be the most budget-friendly. Since permanent adhesive labels create a strong bond with the container they are applied to, removing the label can damage the label or container.
- Removable: Labels with a removable adhesive can be removed for a window of time after application without damaging the label or surface it’s applied on. Removable adhesive labels and stickers are ideal for temporarily marking items, store coupons, and limited-time promotions. Be aware that temperature can affect the stickiness and removable capabilities of labels with this adhesive type.
- Repositionable: Repositionable adhesives are designed for short-term removability in cases where the label needs to be repositioned or reapplied. This adhesive can save you time and resources in the long run when labels need to be removed for repositioning (e.g. a crooked label on a container) or reapplied to another surface without losing much adhesion. Depending on which type of repositionable adhesive is used, it can eventually become permanent. The time between initial application and permanent bonding varies depending on the formulation.
.
Getting Technical: Adhesive Properties
The information above is probably enough to help you understand the type of adhesive that will work best for your situation and our reps are ready to walk you through all the variables that go along with these selections. That said, label adhesives can have varying characteristics even if they’re categorized as the same "type," so for your reading pleasure and curiosity, here is an outline of some of the basic properties that help determine an adhesive’s performance as tested by our material suppliers.
.
- Initial Tack: The immediate holding power of the label adhesive on contact with a specific surface. If the initial tack is low, it will have low adhesion, allowing the label to be removed cleanly. Adhesives with a low initial tack will build-up adhesion over time (i.e. the difference between removable and repositionable). On the flipside, adhesives with high initial tack will have a stronger adhesion and bond to the container much more quickly.
- Ultimate Adhesion: The maximum holding power the label will achieve as the adhesive fully bonds to the surface. How long it takes for an adhesive to gain ultimate adhesion varies and depends on factors like the adhesive’s stiffness, the roughness of the receiving surface and environmental conditions. Depending on those factors, it can take anywhere from 2 – 24 hours for ultimate adhesion to happen.
- Shear Resistance: Simply put, label adhesives with a low shear are soft which allows them to flow into the surface they’re applied. They also have a higher initial tack, but can split apart under stress. A higher shear adhesive is more firm so it doesn’t flow as well into the surface, resulting in a lower initial tack and making it less likely to split apart under stress.
- U.V. Resistance: If your labels will be exposed to ultraviolet (U.V.) light for extended periods, they may be susceptible to colour changes or weakened adhesion. Select a U.V. resistant adhesive in cases where your labels will be exposed to U.V. light on your end, or if your labels will be exposed to U.V. light during the printing process (e.g. when a U.V. laminate or coating is applied to your labels) to minimize these effects.
- Solvent Resistance: The adhesive’s capacity to withstand exposure to solvents like water, alcohol, petrochemical solvents, plasticizers, etc. without losing adhesion. The container contents, along with the environment where the product will be used, should be considered.
- Mandrel Hold: How well the label adhesive holds up to a curved or tight radius surface. If an adhesive has a good mandrel hold, it will be harder for the label’s edges to lift up, also known as "flagging."
- Cold Flow: Temperature is an essential consideration with adhesives. Cold flow refers to the adhesive’s ability to bond (or "flow") to a container at below normal temperatures. "Cold temperature" and "all temperature" adhesives will work best when the label is applied in cold environments.
- Minimum Application Temperature: When an adhesive isn’t designed for cold temperatures, it will stiffen and lose its adhesive strength as the temperature decreases. Most adhesives have a minimum application temperature of 40-50 °F before they crystallize and become solid. Cold temperature adhesives can work in temperatures as low as -20 °F.
- Service Temperature Range: The temperature range the adhesive can function in after the label has been applied and built up to its ultimate adhesion. Most pressure-sensitive adhesives have a range of -65 °F to 200 °F with a paper label stock or up to 300 °F with a film label stock.
.
.
.
Original article from https://consolidatedlabel.com/